To call yourself a watchmaker is a rare privilege.
To be born as one is a curse.
Our journey into watchmaking started in a small central European country in the late 1930s when my grandfather, Mihajlo Hacko, commenced his apprenticeship. By 1951, he was running his own watch repair and retail business. He trained my father in the trade, and my father trained me. Today, I am proud that my son is continuing the family tradition.
The ‘curse’—a solemn utterance to push oneself on the quest
for perfection to the point of suffering—this is what makes
us tick. Yet perfection is unattainable. Even the best, most reputable horological craftsmen can merely hope that their contribution to mechanical art is appreciated as an attempt to merely ‘reduce the imperfection’.
Mihajlo Hacko - 2017
Our Mark II watch is precisely that: an attempt to showcase our ability to shape a metal. To turn a plate of raw titanium into a splash of colour, to create mesmerizing patterns, to form extremely delicate yet fully functional watch components using the most precise machinery, and then to hand finish them to as close to perfect as humanly possible. To continue 400 year old traditions of mechanical horology.
As my grandfather used to say: we are here to serve you.
Nicholas Hacko, 2023

​
Process
01 Design
Every timepiece begins with an
idea. The advantage of having
a small, collaborative team of
watchmakers and CNC machinists
is understanding the possibilities
and limitations of translating designs
into reality. After all, a watchmaker
without CNC skills is just a
dreamer; a CNC operator without
watchmaking knowledge is just a
machinist.
We begin the design process by
brainstorming with our team, and
transferring many hand-drawn
sketches and concepts into
computer-aided-design (CAD) files.
These new 3D files, called
“solids”, are given defined physical
parameters: height, thickness,
clearances, tolerances, angles and
radii. Changing just one parameter
slightly can cause a chain reaction
of revisions, so this is a delicate
process and can take months to
refine. Our Mark II design took more
than 20 iterations.

02 Manufacture

Once a design has been finalised, the next step is transferring the files into CAM software, which creates “tool paths”. This tells the machine which tool to use, where to travel, how to remove material, and at what speed. Multiple tools and operations are required to manufacture every component of a watch, so this CAM file is impossibly complex. A single base dial requires 13 different tools and 29 operations, totalling more than 800,000 lines of code.
While our CNC machines are huge pieces of equipment, cutting tools are tiny. A single tool costs anywhere between $30 to $300, and one tool can be used on only about a dozen parts. In this process, there is no room for mistakes. A mistake on a tool path will immediately break a tool, or cause serious damage to the machine itself.
03 Parts
The dial “set” includes the base dial,
hands, applied numerals, batons
and the nameplate. All of these
components are directly visible, and
demand the highest level of quality.
After all, this is the part of the watch
that you see the most!
Every watch component undergoes
a series of operations on multiple
machines, and passes through
various stages of post-machining
and finishing. Turning, hardening,
polishing and blueing even a single
screw, hand, or applied index takes
significant time and expertise.
In the Mark II, every component in
the dial set is made entirely of Grade
5 Titanium. Grade 5 Titanium is used
prolifically in advanced engineering
applications - from bone implants
and screws, to the compressor
blades of a jet engine, to Formula 1
piston rods.




04 Finishing
All three hands, seconds, minutes and hours, as well as the hour markers—or “batons”—are faceted at a 4 degree angle. Although this is a small angle, this has a massive visual effect, allowing the hands to “dance” in the light and creating a sharp line down their centre.
The facet is also decorated with a totally unique finishing technique called “feathering”. Inspired by the coastal birds found on Sydney’s Northern Beaches—seagulls, sea eagles and sulfur-crested cockatoos—this grinding finish is applied to the hands at a 45 degree angle, to mimic the shape of a feather. To the best of our knowledge, this is the first time such a finish has been used in all of horology.
Feathering is achieved on a machine called a surface grinder. Surface grinding is an extremely accurate method of removing small amounts of material in a controlled manner. It takes years of experience for toolmakers to master this machine. Decades of shared experience enabled our in-house toolmakers to master this process.
​
The type of abrasive wheel used is a critical part of achieving the perfect finish. We tried numerous different combinations of wheel and coolant to arrive at our own Mark II feathering “recipe”. This faceting and feathering technique poses a massive technical challenge. If the facets are off by only 10 micrometers, your eye begins to pick up a lack of symmetry, so it is crucial that all our jigs and raw hand dimensions are checked and kept to a tight tolerance. Further, the feathering creates a complex compound angle that requires a very complex jig, which can take weeks to design and make. Each jig that holds these hands is a consumable, and after about 20-30 hands, needs to be discarded.
Tech Specs
Mark II "Curl Curl"
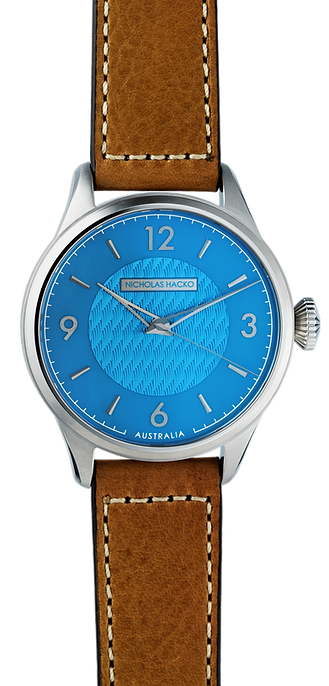

Case
• 40mm case size
• 316L stainless steel
• Double dome sapphire crystal, with double AR coating
• Water resistance to 100m
Dial
• Grade 5 titanium anodised base dial, with guilloche “Curl Curl waves” pattern
• Grade 5 titanium applied numeral with straight graining
• Grade 5 titanium hour markers with “feathered” facetting
• Grade 5 titanium minutes, seconds and hour hands with “feathered” facetting
Movement
• Soprod Automatic M100 movement
• 40 hours power reserve
Warranty + Servicing
• 5 year warranty
• All spare parts held in-stock
Ordering
One of our biggest goals in 2023 is to bring the MKII into stable production, and keep a small number of watches in stock. The challenge for us is that our total production is limited to between 50-100 watches per year across all models. The initial response for the MKII has been fantastic, but it's been a struggle to keep the watch "in-stock".
​
Because of this, availability will fluctuate during the year, as watches are manufactured and assembled they will be allocated at a first come, first served basis.
​
Price: 7,900 AUD
​
Availability: Get in touch!
​
​


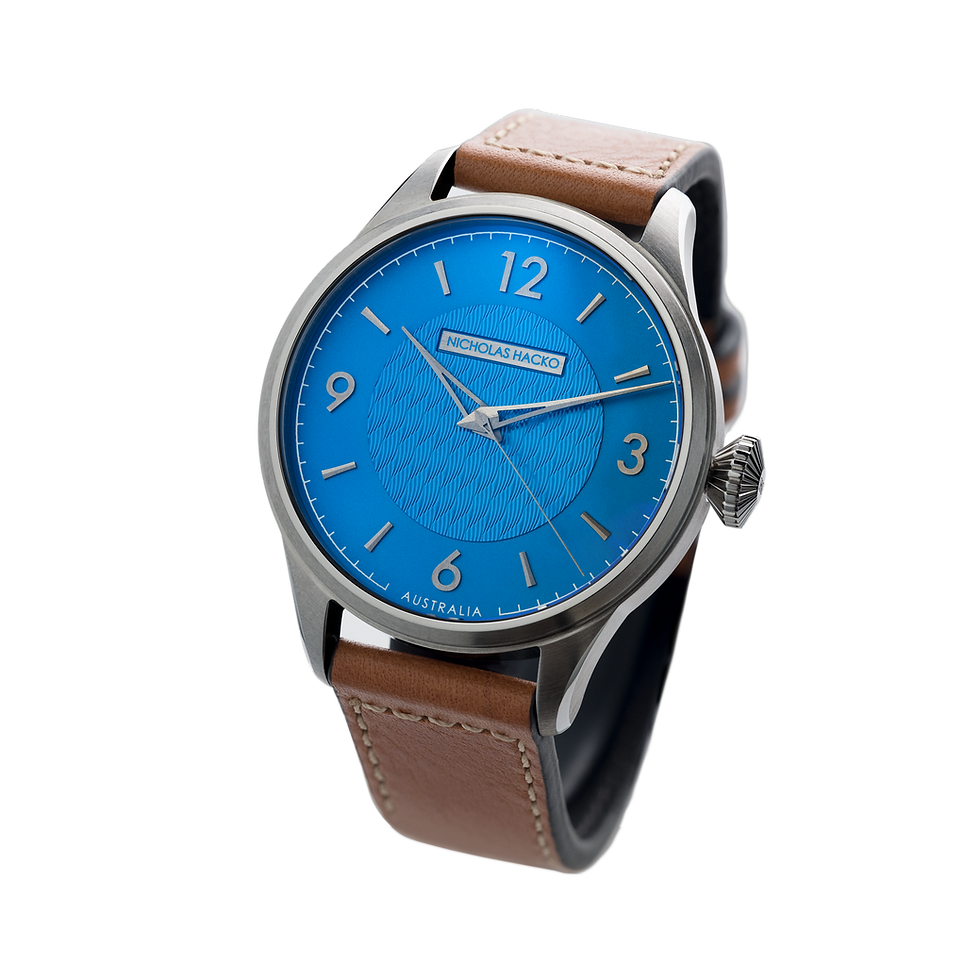
